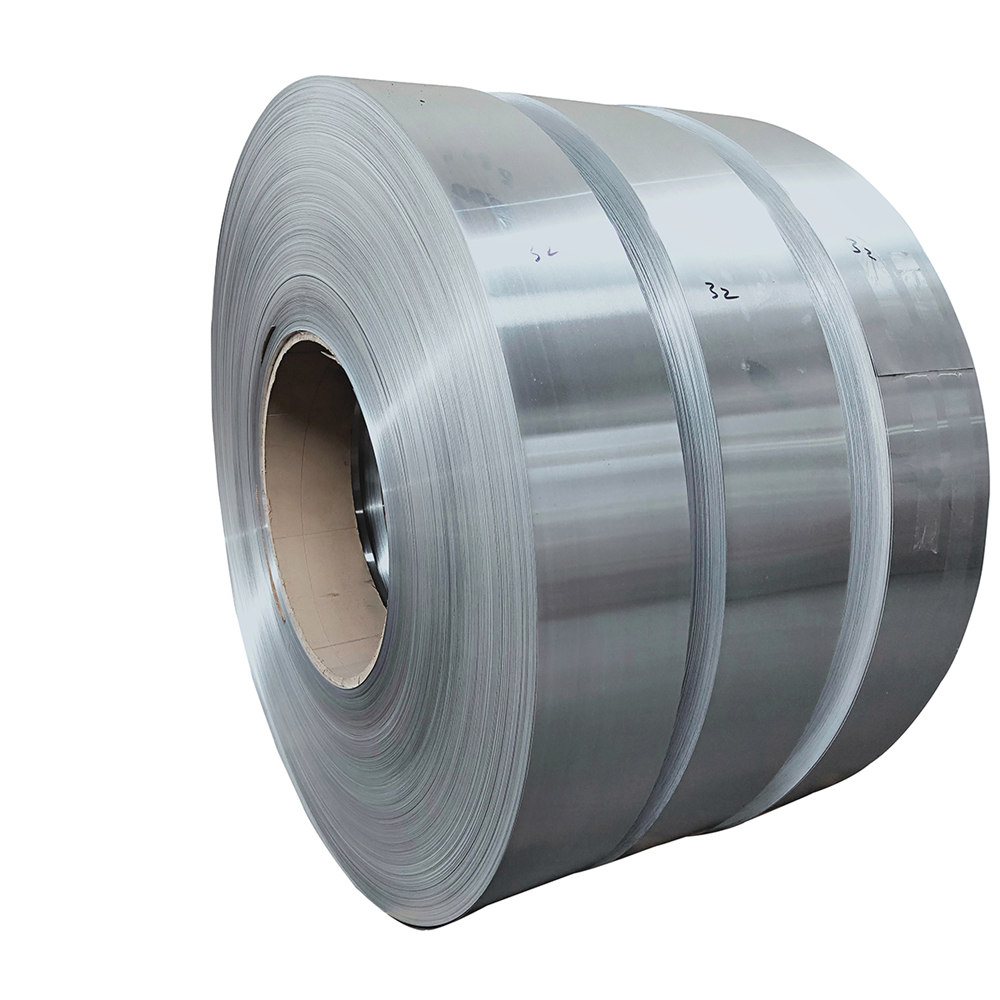
Master Aluminum Extrusion Design: A Comprehensive Guide
Aluminum extrusion is a flexible and efficient way to make many different shapes and profiles out of aluminum alloys. This method can be used in many different fields, like the automotive, aerospace, construction, and consumer goods industries. In this article, we look at the basics of designing aluminum extrusions. We talk about important things like alloys, design considerations, and common uses.
Aluminum Alloys for Extrusion
Choosing the right aluminum alloy is important if you want the final product to have the properties and performance you want. The most common aluminum alloys for extrusion include:
- 6061: Widely used due to its excellent strength-to-weight ratio, corrosion resistance, and weldability. Typical applications include structural components, automotive parts, and aerospace components.
- 6063 is an alloy that is known for its smooth surface and resistance to corrosion. It is used for decorative and architectural purposes, like making window frames, door frames, and furniture.
- 6082: Offers high strength and good corrosion resistance, making it suitable for applications in transportation, structural engineering, and marine environments.
Design Considerations for Aluminum Extrusions
To achieve optimal results in your aluminum extrusion projects, consider the following design factors:
Profile Complexity
- Aim for simplicity and functionality while preserving the desired aesthetics and structural integrity.
- Be mindful that more complex designs may require special tools, increasing costs and lead times.
- Collaborate with your extrusion partner, such as Zeao, to determine the most efficient design approach.
Wall Thickness
- Ensure even material flow during the extrusion process by maintaining a consistent wall thickness.
- A minimum wall thickness of 1mm is generally recommended.
- Thicker sections may necessitate additional support ribs or reinforcements.
Corner Radii
- Incorporate corner radii into your design to distribute stress evenly, reducing the risk of stress concentrations and improving material flow.
- A minimum radius of 0.5mm is recommended for inside corners, while a minimum radius of 1mm should be used for outside corners.
Tolerances
- Set appropriate tolerances to guarantee that the final product meets design requirements while minimizing production costs.
- Be aware that tighter tolerances may increase production costs due to the need for additional machining or finishing processes.
Taking these key design points into account will make your aluminum extrusion projects much more efficient, cost-effective, and successful as a whole. By working with a reliable and knowledgeable extrusion provider like Zeao, you can make sure that these design factors are seamlessly integrated into your projects, which will lead to great final products.
Surface Finish Options for Aluminum Extrusions
Various surface finishes can be applied to aluminum extrusions, enhancing their appearance and providing additional protection against corrosion and wear:
- Anodizing is an electrolytic process that coats the surface with an oxide layer to protect it and give it a variety of colors.
- Powder Coating: A dry finishing process that applies a protective and decorative layer of powder, available in various colors and textures.
- Mechanical Finishing: Techniques such as polishing, brushing, and sandblasting can be used to create different surface textures and appearances.
Common Applications of Aluminum Extrusion
Aluminum extrusions are used in a wide range of industries and applications due to their unique combination of strength, lightness, and design flexibility:
- Automotive: Extrusions can help parts of a car, like the chassis, body structures, and engine parts, be lighter and use less gas.
- Aerospace: Aluminum extrusions are used in airplane frames, seat frames, and other parts because they are strong for how light they are and don't rust.
- Extruded aluminum profiles are used in the construction of window and door frames, curtain walls, and roofing systems because they are strong and can be made to look different.
- Consumer Goods: Aluminum extrusions are used in things like electronics, appliances, and furniture to make them lighter and stronger.
Conclusion
In conclusion, aluminum extrusion design is an important part of the manufacturing process and has a wide range of uses and benefits in many different industries. By knowing the basics of aluminum extrusion design, such as alloy selection, design considerations, surface finishes, and common uses, engineers and designers can make high-quality, cost-effective, and versatile products that meet specific needs and stand the test of time.
As aluminum extrusion technology keeps getting better, new and interesting uses are always being found. If you keep up with the latest changes and trends in this field, your projects will always be at the cutting edge of design, performance, and sustainability.
Future Trends in Aluminum Extrusion
As technology and ways of making things change, aluminum extrusion is likely to become more important in many industries. Some of the future trends in aluminum extrusion design include:
-
Sustainable Manufacturing: As the focus on eco-friendly practices grows, the aluminum extrusion industry is likely to adopt more environmentally friendly ways to make things, such as using more recycled materials and making things in a way that uses less energy.
-
Innovative Applications: As a result of advancements in material science, engineering, and design, new applications for aluminum extrusions will continue to appear. This will open up new markets and opportunities for aluminum extrusion products.
-
Integration of Smart Technologies: Adding smart technologies like sensors and Internet of Things (IoT) devices to the designs of aluminum extrusions will let them do new things and improve how well they work.
-
Advanced Surface Treatments: When new surface treatments and finishes are made, they will allow for more customization and better performance, such as better resistance to corrosion and wear.
By keeping up with these trends and always learning more about how to design with aluminum extrusion, you can make sure that your projects stay innovative, competitive, and useful in a world that is always changing.