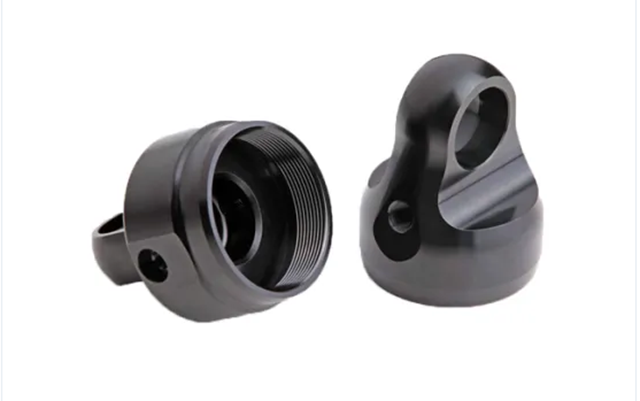
CNC parts processing type how to do the clamping workpiece
“Operators began to make feed speed CNC machining parts transferred to the small, single section, rapid positioning, falling knife, feed must concentrate, when there is something wrong with the hand should be put on the stop button to immediately stop, watch tool motion direction to ensure the safety of feed, then slowly increase the feed rate to the right, at the same time to the cutting tool and workpiece cooling fluid or air cooling.”
Operators began to make feed speed CNC machining parts transferred to the small, single section, rapid positioning, falling knife, feed must concentrate, when there is something wrong with the hand should be put on the stop button to immediately stop, watch tool motion direction to ensure the safety of feed, then slowly increase the feed rate to the right, at the same time to the cutting tool and workpiece cooling fluid or air cooling.
Do not leave the control panel too far when the rough machining, abnormal phenomena in time to stop the inspection.Pull the table again after roughening to make sure the workpiece is not loose.If so, recalibration and hits are required.Continuous optimization of processing parameters in the process of processing, to achieve better processing effect.
After the workpiece is finished, it shall be measured whether the main size and value are consistent with the requirements of the drawing. If there is any problem, it shall be immediately notified to the shift leader or programmer for inspection and solution. After passing the self-inspection, it can be removed and must be sent to the inspector for special inspection.The common CNC parts processing types are as follows:
1, hole processing: before drilling in the processing center must be positioned with the center drill, and then drill with 0.5~2mm smaller than the size of the drawing, with the appropriate bit finishing.
2, reaming processing: the workpiece reaming processing is also to use the center drill positioning, and then use 0.5~0.3mm smaller than the drawing size of the drill hole, reamer reaming, reaming pay attention to control the spindle speed in the reaming process within 70~180rpm/min.
3, boring processing: for the workpiece boring processing to use the center drill positioning, and then use 1~2mm smaller than the drawing size of the drill hole, and then use a rough boring tool (or milling tool) processing to only one side about 0.3mm machining margin, after the fine boring tool with pre-adjusted size for fine boring, after a fine boring margin shall not be less than 0.1mm.
4, direct numerical control (DNC) operation: before the DNC CNC machining to install the workpiece, set a good zero, set good parameters.Open the machining program to be passed in the computer to check, and then let the computer into the DNC state, and enter the correct machining program filename.Press TAPE key and program start key on the machine tool, then the machine tool controller appears flashing LSK words.Press enter keyboard on the computer can be DNC number processing.
In the process of CNC parts processing workpiece clamping is also a problem must be paid attention to, the workpiece clamping in the process of processing how to do this step?
Before the workpiece clamping to clean the surface, do not adhere to oil, iron and dust, and use a file (or whetstone) to remove the burr on the surface of the workpiece.
The high-speed rail used for clamping must be ground by grinding machine to make the surface smooth and flat.Iron, nuts must be strong, reliable clamping workpiece, some difficult to clamp the small workpiece can be directly clamped on the vice;The machine tool working table should be clean and clean, without iron scrap, dust, oil;Mat iron is generally placed in the four corners of the workpiece, the workpiece with a large span in the middle of the need to add such a high mat iron.
According to the drawing size, use caliper to check the length, width and height of the workpiece.
When clamping the workpiece, according to the programming work instruction of the clamping and placing way, to avoid the processing parts and in the processing of the tool head may encounter the fixture.
After the workpiece is placed on the mat, it is necessary to pull the drawing according to the requirements of the workpiece datum level, for the workpiece has six sides are grinding to check whether its verticality is qualified.
After the completion of the workpiece drawing table must tighten the nut, in order to prevent the clamping is not firm and the workpiece in the processing of the shift phenomenon;Pull the table again to ensure that the clamping error is not out of tolerance.