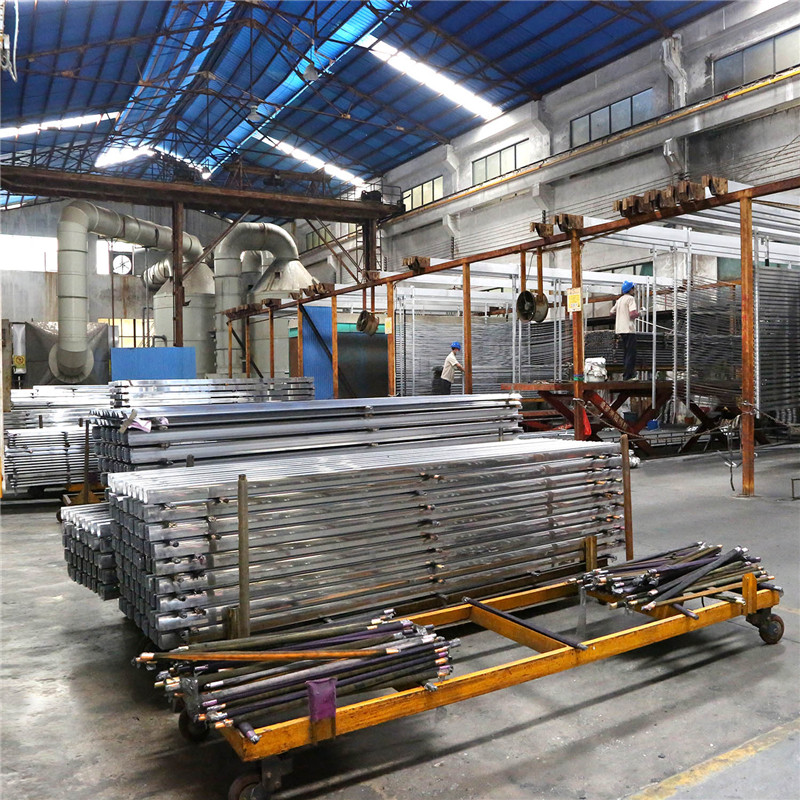
Benefits of Using Aluminum Extrusions in Automotive Manufacturing
In the competitive world of automotive manufacturing, companies are always looking for ways to improve their processes and products. One method that has gained popularity in recent years is the use of aluminum extrusions. In this article, we will explore the benefits of using aluminum extrusions in automotive manufacturing and how it can help companies like Zeao stay ahead of the game.
What are Aluminum Extrusions?
Aluminum extrusions are a way of making things out of aluminum by shaping it into different shapes and profiles. In this process, heated blocks of aluminum are pushed through a die to make a certain shape. The result is a material that is light, strong, and easy to work with. It can be used for many things, including making cars.
The Benefits of Using Aluminum Extrusions in Automotive Manufacturing
Lightweight
One of the main benefits of using aluminum extrusions in automotive manufacturing is its lightweight nature. Compared to traditional materials like steel, aluminum extrusions can weigh up to 60% less. This can lead to significant fuel savings, which is important in today's world where fuel efficiency is a top priority.
Strength
Despite its lightweight nature, aluminum extrusions are incredibly strong. They have a high strength-to-weight ratio, which means they can withstand heavy loads and stress without compromising their structural integrity. This makes them an ideal material for automotive applications where strength is crucial.
Versatility
Another benefit of using aluminum extrusions in automotive manufacturing is their versatility. Aluminum extrusions can be shaped into a variety of profiles and shapes, making them ideal for use in a variety of automotive components. They can be used for everything from body panels to suspension components, and everything in between.
Corrosion Resistance
Aluminum extrusions are also very resistant to corrosion, which makes them perfect for use in car parts that are often exposed to the weather. Aluminum doesn't rust or corrode like steel does, which can make parts last longer and lower maintenance costs.
Cost-Effective
Finally, using aluminum extrusions in automotive manufacturing can be cost-effective in the long run. Even though aluminum extrusions may cost more up front, their low weight and resistance to corrosion can save a lot of money over the life of a part or vehicle. Additionally, their versatility can lead to reduced tooling costs and faster production times.
FAQs about Using Aluminum Extrusions in Automotive Manufacturing
Is aluminum extrusion more expensive than traditional materials like steel?
Even though aluminum extrusions may cost more up front, their low weight and resistance to corrosion can save a lot of money over the life of a part or vehicle.
Are aluminum extrusions as strong as steel?
Even though aluminum extrusions are light, they are very strong and have a high strength-to-weight ratio. This makes them a great choice for applications in the automotive industry where strength is very important.
Can aluminum extrusions be used for a variety of automotive components?
Yes, aluminum extrusions can be shaped into a variety of profiles and shapes, making them ideal for use in a variety of automotive components. They can be used for everything from body panels to suspension components, and everything in between.
Conclusion
As we have seen, there are many benefits to using aluminum extrusions in automotive manufacturing. Aluminum extrusions are better than traditional materials like steel in many ways, from how light they are to how strong and flexible they are. Aluminum extrusions can help companies like Zeao stay competitive in the fast-paced world of automotive manufacturing by being added to their manufacturing processes.